From Thread to Tote: The Step-by-Step Process of Making WSDO's Cotton Bags
WSDO: The Process of Making Hand-Woven Cotton Bag in Nepal
Have you ever wondered how WSDO (Women’s Skills Development Organization)'s hand-loomed cotton bags are made?
From sourcing raw materials to the final product, the entire process takes at least a week and involves ten intricate steps.
In this article, we'll take you through the journey of how WSDO's cotton bags are made.
Raw Materials Procurement
WSDO imports 100% cotton thread from India and works with local women in the village of Shalija to purchase the beige, strong fabric known locally as Allo. Allo is a plant fiber similar to ramie that grows in Nepal between 1500 and 3000 meters above sea level. After repeated washings, this strong vegetable fiber becomes soft enough to be spun into yarn.
Dyeing and Drying
The cotton thread is boiled and dyed using Azo-free certified dyes. The used dye wastewater is filtered before being disposed of. The cotton is then dried in the sun. The vibrant colors add a therapeutic and interesting touch to the process.
Balling
After dyeing and drying, the cotton thread is rolled into a ball for easy storage.
Looming
Women organize and arrange cotton threads of different colors on the loom according to the pattern and width of the fabric to be woven. They then tie the loom around their waists to prepare for the weaving process.
Weaving
Artisan women use backstrap looms to weave intricate designs for final products, with a target length of 7 meters and varying widths (4cm-40cm) suitable for different purposes (e.g. bag straps, cross-body bags, backpacks, large tote bags). On average, each piece takes 3-4 days to complete.
Artisans can work at home and balance household, child care, and farm work while earning extra income. This flexible arrangement is stable and long-lasting.
During the pandemic, all looms were distributed for home use to avoid cluster infection.
Designing
Ganapati Crafts Co. partnered with WoVen Workshop to create exclusive designs. Yian, the founder of Ganapati Crafts Co., hand-painted the sketches and visits the Pokhara workshop every year to collaborate with the samplers. Bags are made on-site to meet American aesthetics and usage habits.
Cutting
The artisans trace the desired bag shape onto the handwoven fabric with chalk, following a template, and then cut the pieces out with large scissors, readying them for tailoring.
Sewing
The cut pieces of fabric are then passed to talented tailors who transform them into stunning bags through their sewing expertise.
Quality Control
Once the product is finished, it undergoes a thorough examination by the quality control manager. If any defects or shortcomings are found, it is sent back to the tailor for rectification to guarantee that the product meets consumer expectations in terms of quality stability.
Packing and Shipping
Following at least nine extensive handcrafted procedures, the final product is transferred to the shipping department for packaging and shipping evaluation. The product is then dispatched internationally to Ganapati Crafts Co. where the team performs again a thorough quality check, plans the display, and presents it appealingly to customers.
Author
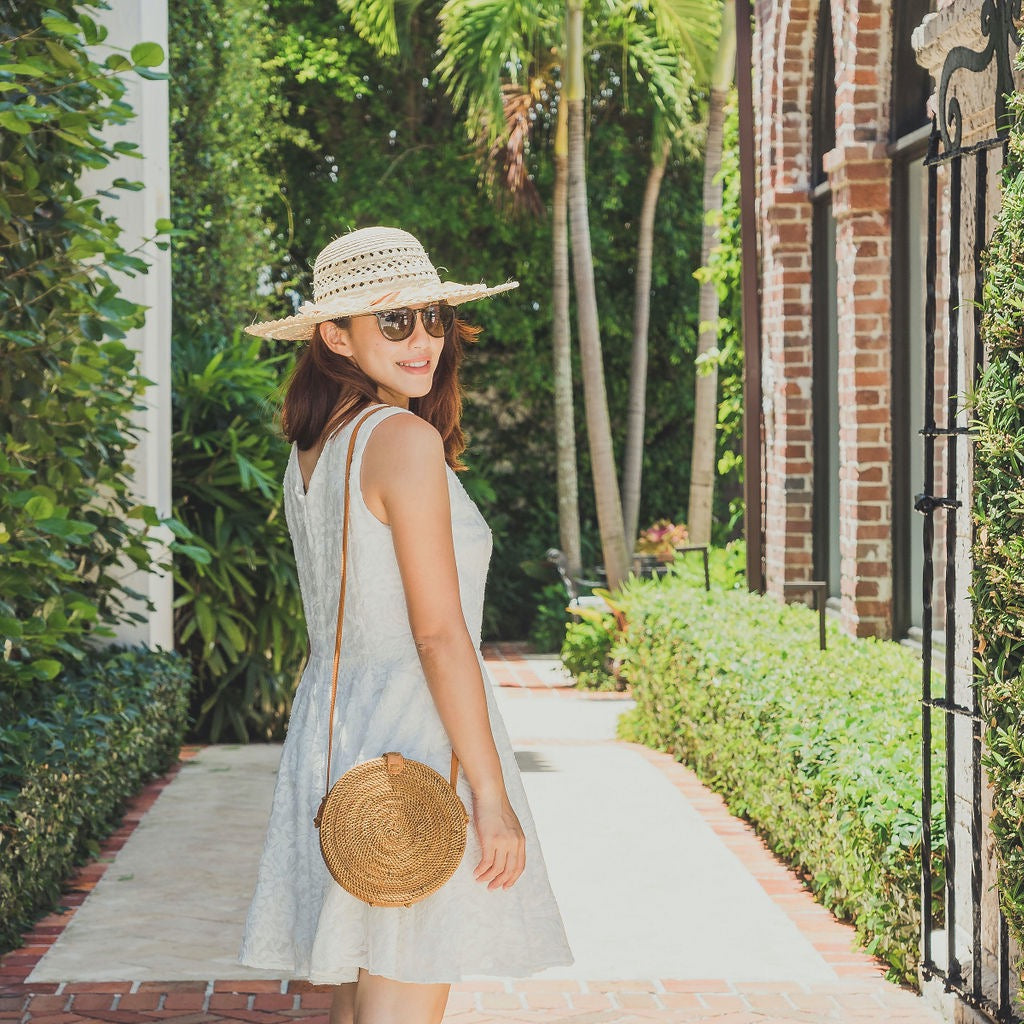
Miss Yian
Owner of Ganapati Crafts Co.
Yian, a Taiwanese Floridian, operates as a handicraft vendor, offering a range of charming and unique products including felt finger puppets, nursery decor, holiday ornaments, and handwoven bags. Be sure to visit Yian's brand, Ganapati Crafts Co., to explore her creative and one-of-a-kind creations.